The industrial sector seems to be tapping into the advantages of 5G wireless networks at a slower pace than the leaps 5G technology is taking. Exceptions are some large global companies in the automotive, aerospace or logistics spaces, and some large industrial infrastructures, such as ports and mines. With research and investment, these industries are embracing the advantages of 5G’s ultra-reliability, ultra-low latency, real-time at the edge and the richness of the spectrum, which includes millimeter waves (mmWave).
5G was designed from the ground up, almost ten years ago, with ultra-reliability, low latency and a broad range of spectrum options in mind to meet the demanding requirements of Industrial IoT (IIoT) and industrial automation. In campus networks with mmWave spectrum, 5G delivers these benefits: first and foremost, for standard and safety control applications where data originates in numerous industrial sensors, actuators and controllers. 5G can “augment” and even replace traditional wired industrial network connections – a game changer in terms of cost, flexibility, time-to-market and sustainability for industrial operations globally.
Adopting more sustainable policies is good for business in many verticals. One example are tethered fixed industrial assets (skids, machines or equipment), which require costly wired infrastructure for any new installation. The material usage need negatively impacts sustainability initiatives. Of no lesser importance is the time and material cost of retooling fixed industrial assets to respond to fast-changing market conditions.
Agility is much needed in the manufacturing industry where, as an example, volatile supply chains have needed to be reorganized rapidly much more than in the past.
The networks that provide connectivity are a key element of the digital transformation towards an intelligent industrial production, and the 5th generation of wireless, the more so when in the layout of a private industrial network, is a material trigger for the digitization of an entire industrial operation, as well as a driver for material steps forward as to agility and sustainability.
Sustainability is paying off, in particular in the automation segment, because it creates resilience, as the Future of Enterprise 3rd Edition – Time to Rethink Resilience concludes.
Important use cases in smart manufacturing are firstly all those applications in which operators need to have maximum visibility and intelligence by using analytics, digital twins and augmented reality (AR). Other use cases for 5G are those where mobile applications and assets require an immediate response and “augmented” efficiency, as is the case with automated guided vehicles (AGVs) and autonomous mobile robots (AMR). Other use cases for untethered assets are industrial facilities with static machinery or static equipment with rotating parts (slip-ring replacement) and nomadic equipment (operational while static, non-operational while mobile).
In Rockwell Automation, Ericsson, Qualcomm and Verizon’s testbed, see image below. the tests were run according to a well-established test plan provided by Rockwell Automation with strict success criteria of zero faults. It outlined a series of test cases to establish reliable EtherNet/IP standard and safety (CIP Safety™) I/O connections from the GuardLogix® safety controller. Twelve distributed areas with FLEX 5000® standard and safety I/O, representing skids, machines or equipment. Note, the purpose of the safety controller in each distributed area was to collect testbed telemetry data only.
Ericsson contri
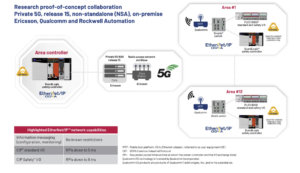
Il test: Ethernet assieme a wireless 5G per l’automazione sono perfettamente compatibili nelle reti private industriali 5G.
buted with the radio access network (RAN) infrastructure, composed of a mmWave base station using 28 GHz (n261) and LTE band 2 using Release 15, and Private 5G core (3GPP Release-15, non-standalone (NSA), on-premise).
Qualcomm’s MTP mobile test platform for data collection and traffic flow analysis, was used also as industrial 5G to Ethernet adapter.
Verizon’s thought leadership in industrial networking innovation with 5G was an important contribution towards defining requirements, target feature sets and scope of the testbed, including a roadmap of future validation requirements.
The conclusions of the research and tests confirm, first of all, that if plants are to be data-driven, a solid connectivity architecture must be in place.
More specifically, the partner companies underlined that the Ethernet/IP is ready for industrial private 5G; also, as Ethernet/IP standard and safety applications are concerned.
The research collaboration will continue. There are plans to evaluate EtherNet/IP time synchronization (CIP Sync™) and distributed motion (CIP Motion™) applications over 3GPP Release 16 standalone (SA) Industrial Private 5G. The results of an initial proof-of-concept on a prototype testbed were promising.
In summary, as Gregory Wilcox explained to me at Automation Fair 2022 in Chicago, thanks to Rockwell Automation, Ericsson, Qualcomm Technologies Inc. and Verizon’s testbed, real 5G enabled industrial automation test cases work as promised, progressing in the path towards smart manufacturing.